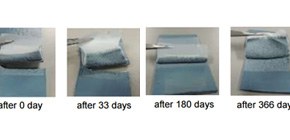
Lifetime of surface modification of polytetrafluoroethylene (PTFE) extended
Will expand applications of PTEF
Generally, the lifetime of the surface of plasma-treated polytetrafluoroethylene (PTFE) is very short. Because of the short lifetime of surface modification, adhesion had to be performed immediately after plasma treatment, which was a great disadvantage for practical applications of plasma treatment.
A group of researchers led by Associate Professor YAMAMURA Kazuya and Assistant Professor OHKUBO Yuji at the Research Center for Ultra-Precision Science and Technology, Osaka University, together with Researchers SHIBAHARA Masafumi, NAGATANI Asahiro, and HONDA Koji at the Hyogo Prefectural Institute of Technology, succeeded in increasing the adhesion strength of PTFE by using atmospheric pressure plasma treatment under heating (heat-assisted plasma treatment) and keeping the lifetime of the surface modification for one year or longer, a world first.
Previously, when the surface of PTFE was modified by plasma treatment, if adhesion was not performed immediately following plasma treatment, the adhesion strength decreased because of the short lifetime of surface modification.
This group demonstrated that PTFE strongly adhered to rubber even if thermocompression was performed to PTFE one year after plasma treatment, verifying that the lifetime of surface modification was very long. It was confirmed that the wettability to water of PTFE treated with heat-assisted plasma treatment didn’t change a year after the treatment and that 80 percent or more of peroxide radicals produced by plasma treatment remained a year after the treatment.
This group’s achievement has eliminated the need to adhere in a rush after plasma treatment, drastically easing restrictions on the adhesion process. Heat-assisted plasma treatment has made it possible to keep the adhesion strength of PTFE. This will allow companies without plasma treatment devices to use PTFE with excellent adhesion and lead to the expansion of applications of PTFE. Applications to resin other than PTFE will also be discussed in the future.
Abstract
A polytetrafluoroethylene (PTFE) surface was modified using atmospheric pressure plasma treatment under heating (heat-assisted plasma treatment) to promote its direct adhesion to isobutylene–isoprene rubber (IIR) without any adhesives. Plasma-treated PTFE and unvulcanised IIR were thermally compressed and their adhesion strength was evaluated via a T-peel test. Heat-assisted plasma treatments conducted above 250 °C drastically increased the adhesion strength over 2.0 N mm −1 before IIR failure. The plasma-treated PTFE surface was evaluated using X-ray photoelectron spectroscopy, nanoindentation and scanning electron microscopy. The results of these analyses indicated that the adhesion strength drastically increased because heat-assisted plasma treatment promoted the formation of carbon–carbon crosslinks and/or etching of a weak boundary layer (WBL) on the PTFE surface. This led to the recovery of the WBL in PTFE, which resulted in the prevention of PTFE inter-layer peeling in the WBL. In addition, the estimated lifetime of the surface modification surprisingly exceeded one year.
Figire 1. Long lifetime of high adhesion property of heat-assisted plasma-treated PTFE. White: fluoropolymer sheet, Blue: isobutylene–isoprene rubber (IIR).
To learn more about this research, please view the full research report entitled “ Adhesive-free adhesion between polytetrafluoroethylene (PTFE) and isobutylene–isoprene rubber (IIR) via heat-assisted plasma treatment ” at this page of the RSC Advances website.
Related links
- Research Center for Ultra-Precision Science & Technology (link in Japanese)
- Ultra-Precision Science & Technology (link in Japanese)
- Development of a technique enabling fluorine-containing resin to adhere strongly to a metal film
- Success in affixing fluoropolymer to Isobtylene-isoprene Rubber without using adhesive
- A technique enabling fluorine-containing resin to adhere strongly to a metal film without using adhesive