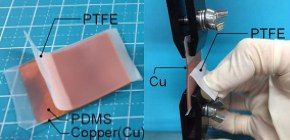
Give It the Plasma Treatment: Strong Adhesion without Adhesives
Researchers bond polymers to glass and metal by using surface chemistry rather than adhesives, opening doors to potential use in food production and medicine
Polymers containing plastics are essential in modern life. Being lightweight, strong and unreactive, a vast range of technologies depend on them. However, most polymers do not adhere naturally to other materials, so they need adhesives or corrosive chemical treatments to be attached to other materials. This is a problem in areas like food and medicine, where contamination must be avoided at all costs.
A clean way to make industrial polymers adhesive is urgently needed. Now, a team at Osaka University has achieved just that. They have developed a suite of plasma treatments to allow vulcanized rubber and the plastic PTFE (polytetrafluoroethylene) to adhere to one another, or to other materials. The method activates the polymers’ surface chemistry, as described in a study in Scientific Reports.
“If you spray PTFE with a plasma of helium at 200 degrees, it can adhere to unvulcanized rubber—this is a technique we developed earlier in our lab,” says study lead author Yuji Ohkubo. “But vulcanized rubber presents a greater challenge. In our latest study, we customized a new plasma treatment for vulcanized silicone rubber, making it adhere strongly to PTFE for the first time.”
The silicone in question was PDMS (polydimethylsiloxane), a well-known resin. While the key breakthrough in PTFE adhesion was the heat-assisted plasma treatment, the trick with PDMS is to bombard the surface with a plasma jet , by forcing nitrogen/air plasma through a small hole. The jet breaks the silicon–carbon bonds on the surface and converts them to silanol (Si–OH).
Being more reactive than the original silicone surface, these silanol groups can bond with PTFE. Under high pressure, hydrogen bonds form between silanol and the oxygen-containing functional groups on the treated PTFE. Strong covalent bonds (C–O–Si, where C comes from PTFE and Si from silicone) further stitch the two polymers together, even with no adhesive.
Uniting the two materials allows each to enjoy the benefits of the other—the chemical resistance, dirt-repellent and slide-ability of PTFE, and the elasticity of silicone. Opaque PTFE can also be replaced by PFA (perfluoroalkoxy alkane) if transparency is needed. And that’s not all—when the reverse side of the PDMS is also plasma-jetted, it can bond to copper and even glass. Like an extremely strong double-sided tape, this three-layer sandwich allows the fluoropolymers to adhere cleanly to other useful materials.
“PDMS is widely used in medicine, for example in microfluidic chips,” explains co-author Katsuyoshi Endo. “There could be huge benefits in making both PTFE and PDMS more versatile for medical and food technologies through adhesive-free adhesion. Combined with the lack of any need for volatile chemicals, we hope our method will broaden the horizons for polymers in high technology.”
Figure 1. Photograph of three-layer assemblies of (a) PTFE/PDMS/Cu, (b) PTFE/PDMS/SUS430, and (c) PTFE/PDMS/glass. When the PTFE or PDMS sheet was jerked and shaken, no peeling occurred at the interfaces of PTFE/PDMS, PDMS/Cu, PDMS/SUS430, and PDMS/glass. This shows that PJ-treated PDMS could be used as an alternative to strong adhesives to adhere fluoropolymers to other types of materials. (Credit: Osaka University)
Figure 2. Preparation procedure for a two-layer assembly such as PTFE/PDMS (steps 1–3) and a three-layer assembly such as PTFE/PDMS/Cu (steps 1–6). PFA/PDMS, PFA/PDMS/glass, PTFE/PDMS/glass, and PTFE/PDMS/SUS430 assemblies were prepared in the same way. (Credit: Osaka University)
The article, “Adhesive-free adhesion between heat-assisted plasma-treated fluoropolymers (PTFE, PFA) and plasma-jet-treated polydimethylsiloxane (PDMS) and its application,” was published in Scientific Reports at DOI: https://doi.org/10.1038/s41598-018-36469-y .
Related links
- Success in affixing fluoropolymer to Isobtylene-isoprene Rubber without using adhesive
- A technique enabling fluorine-containing resin to adhere strongly to a metal film without using adhesive
- Lifetime of surface modification of polytetrafluoroethylene (PTFE) extended
- Reseasrch Center for Ultra-Precision Science & Technology, Graduate Schoolof Engineering, Osaka University (link in Japanese)