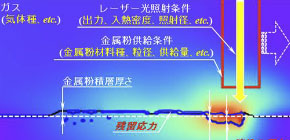
System to evaluate laser irradiation conditions prior to laser coating
Will make laser processing technology user-friendly
A group of researchers from the Japan Atomic Energy Agency (JAEA) and the Joining and Welding Research Institute at Osaka University developed a general-purpose three-dimensional thermohydraulics numerical simulation code, SPLICE, which can evaluate the melting and solidifying phenomena of various metals by laser irradiation on a general engineering workstation.
Laser coating is a technology for depositing high quality coating films by concurrently injecting powder on a substrate and irradiating with laser beams. It is notable that laser coating allows for the deposition of a different metal film on the metal substrate, providing different mechanical properties as well.
However, in order to form a coating film that meets the requirements, powder feed and laser output should be determined appropriately according to the combination of the substrate material and powder material, requiring a large amount of time and labor.
Laser coating technology is currently being developed, eventually aiming to be marketed as a product. The primary challenge in its marketing is making it an easy-to-use technology for anyone. Thus, the researchers developed the general purpose three-dimensional thermohydraulics numerical simulation code SPLICE, reducing computation load while securing computational accuracy.
Through calculations, SPLICE evaluates properties -- penetration depth necessary for a desired coating thickness and coating thickness of the allowable penetration depth – within a few weeks, while conventional methods had required a few months to do so.
In addition, the researchers also evaluated the melting and solidification of solid metals by X-ray imaging at the synchrotron radiation facility SPring-8, confirming the validity of this technology. This group’s achievements will expand the market of upcoming laser coating devices in the industry.
Figure 1
Figure 2
Related link