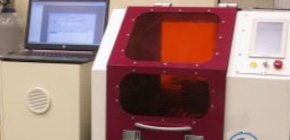
Additive manufacturing (3D printing) with blue direct diode laser developed, a world first!
Will be applied to processing of parts required in various industries
In The New Energy and Industrial Technology Development Organization (NEDO) project, a group of researchers led by Professor TSUKAMOTO Masahiro at the Joining and Welding Research Institute, in cooperation with Shimadzu Corporation, Nichia Corporation, and Muratani Machine Inc., developed the world's first additive manufacturing system (3D printer) for pure copper with high-brightness blue semiconductor laser.
Additive Manufacturing, also referred to as 3D Printing, a technology to produce three-dimensional parts layer by layer from a material, is anticipated to create innovation in manufacturing objects with complex shapes that cannot be made by other methods and achieve limited production of products that respond to diversified customer needs in various fields. Although aviation, space, and electric car industries have a high hope for manufacturing and processing of pure copper materials, conventional 3D printing processes that use near-infrared lasers had challenges in melting such materials.
This group developed a high-brightness blue direct diode laser that can produce a laser power output of 100 watts (W) required for melting pure copper powder. By emitting a blue direct diode laser with a wavelength of 450 nm from an optical fiber with a-100μm-diameter core, it has become possible to focus light to a 100 mm-diameter spot. The power density on the 100 mm-diameter spot at output power of 100W became 1.3×10 6 W/cm 2 , which was enough to melt pure copper powder.
Next, this group developed the Selective Laser Melting (SLM) 3D printer with the focusing head of a high-brightness blue direct diode laser placed inside the body as shown in Figure 1 . With this 3D printer, they achieved the additive manufacturing of pure copper. This 3D printer uses a focusing head instead of a galvanometer mirror, which brings down overall cost.
This technology will be used in the processing of parts for aviation, space, and electric car industries that require additive manufacturing of materials such as pure copper. Additive manufacturing was difficult to achieve by conventional 3D printers that use near-infrared lasers. In addition, SLM 3D printers can achieve more precise fabrication than Laser Metal Deposition (LMD) 3D printers, so this group’s technique will also be used to produce pure copper heat sinks with complex structure.
This group’s technique has enabled additive manufacturing of pure copper, which is more electrically and thermally conductive and difficult to melt with laser irradiation. The technique will be used for processing parts for aviation, space, and electric car industries.
Figure 1
Figure 2
Figure 3
Related link