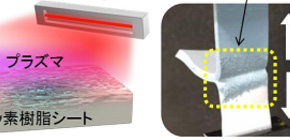
Osaka University Researchers Make the Slipperiest Surfaces Adhesive
Osaka University-led research team develops new way to make non-stick fluoropolymers adhesive using heat and plasma
The convenience of non-stick, Teflon-coated cookware is appreciated in kitchens worldwide, particularly by anyone doing the washing up. The chemical making up Teflon, polytetrafluoroethylene or PTFE, is one of the slipperiest materials known. Outside the kitchen, the low-friction surfaces and high chemical resistance of PTFE are essential to many applications across a range of industries. However, despite its usefulness, PTFE is difficult to work with. Making PTFE adhere to other types of materials requires harsh chemicals.
Now, a research team centered at Osaka University has developed a new way to make PTFE adhesive, and drastically improved the strength of its bonding with other materials. The findings were reported in Scientific Reports.
“People have been looking at how plasma treatments affect PTFE for some time, but no one has really examined how the treatments affect adhesion properties,” study lead author Yuji Ohkubo explains. “With our plasma treatment, we improved the adhesion of the PTFE to some extent, but it was only when we combined this with extra heating of the PTFE that we saw it strongly adhering to rubber.”
The team showed that adding a heating element to the chamber during the plasma treatment, to heat the PTFE, changed the surface structure, making it much harder. The heat and plasma-treated PTFE strongly adhered to the rubber surfaces.
“The real advantages of this work are that it avoids using some nasty chemicals and is relatively simple to implement,” coauthor Kazuya Yamamura says. “In industrial processes, adding a heater to a plasma chamber is much easier than trying to adjust the temperature through the plasma power. We hope this new technique allows PTFE to be used in new ways that just weren’t possible or practical before.”
Abstract
The heating effect on the adhesion property of plasma-treated polytetrafluoroethylene (PTFE) was examined. For this purpose, a PTFE sheet was plasma-treated at atmospheric pressure while heating using a halogen heater. When plasma-treated at 8.3 W/cm 2 without using the heater (Low-P), the surface temperature of Low-P was about 95 °C. In contrast, when plasma-treated at 8.3 W/cm 2 while using the heater (Low-P+Heater), the surface temperature of Low-P+Heater was controlled to about 260 °C. Thermal compression of the plasma-treated PTFE with or without heating and isobutylene−isoprene rubber (IIR) was performed, and the adhesion strength of the IIR/PTFE assembly was measured via the T-peel test. The adhesion strengths of Low-P and Low-P+Heater were 0.12 and 2.3 N/mm, respectively. Cohesion failure of IIR occurred during the T-peel test because of its extremely high adhesion property. The surfaces of the plasma-treated PTFE with or without heating were investigated by the measurements of electron spin resonance, X-ray photoelectron spectroscopy, nanoindentation, scanning electron microscopy, and scanning probe microscopy. These results indicated that heating during plasma treatment promotes the etching of the weak boundary layer (WBL) of PTFE, resulting in a sharp increase in the adhesion property of PTFE.
Fig.: Effect of heating during plasma treatment on adhesion strength (Blue: isobutylene–isoprene rubber (IIR), White: fluoropolymer sheet) (credit: Osaka University)
To learn more about this research, please view the full research report entitled “ Drastic Improvement in adhesion property of polytetrafluoroethylene (PTFE) via heat-assisted plasma treatment using a heater ” at this page of the Scientific Reports website.
Related links
- Department of Precision Science & Technology, Graduate School of Engineering, Osaka University
- Research Center for Ultra-Precision Science & Technology, Osaka University
- Research Center for Ultra-Precision Science & Technology (link in Japanese)
- Hyogo Prefectural Institute of Technology (link in Japanese)
- Development of a technique enabling fluorine-containing resin to adhere strongly to a metal film
- Success in affixing fluoropolymer to Isobtylene-isoprene Rubber without using adhesive
- A technique enabling fluorine-containing resin to adhere strongly to a metal film without using adhesive
- Lifetime of surface modification of polytetrafluoroethylene (PTFE) extended