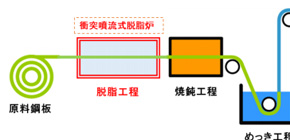
Ammonia combustion technology for reducing CO2 emission in industrial furnaces developed
A group of researchers from Taiyo Nippon Sanso Corporation, Nisshin Steel Co. Ltd., and Osaka University, developed a burner for ammonia combustion that can be used for pretreatment for continuous production of galvanized steel sheets. This group also verified that methane combustion with 30% of ammonia increased energy efficiency and cut CO 2 emission by 50%, compared to existing continuous furnaces.
Steel sheets used for exterior panels of cars and home appliances as well as construction materials are galvanized after cleaning the oil on the surface of a steel sheet in an alkali degreasing step or in a non-oxidizing furnace. Previously, the introduction of jet impingement degreasing furnaces using city gas (methane) made the alkali degreasing step and part of the non-oxidizing furnace unnecessary, making the process simple.
This time, this group developed a burner that enables methane combustion with ammonia. In its performance assessment, when the content of ammonia in co-combustion increased, temperature distribution at various points on the surface of the steel sheet was uniform at the content of ammonia of 10%, 20%, and 30%, and the amount of heat was the same as that of single methane combustion at 400°C.
This group performed the assessment of heat treatment conditions for steel sheets and the state of their surface as well as the assessment of galvanization in methane-ammonia combustion. As a result, they confirmed that it was possible to achieve a level of degreasing, either equaling that achieved by methane combustion or surpassing that achieved by alkali degreasing, through optimization of conditions of combustion.
In the future, it will likely become possible to achieve zero CO 2 emission in single ammonia combustion by using ammonia from hydrogen derived from renewable energy.
Figure 1
Figure 2
Figure 3
Figure 4
Figure 5
Figure 6
Related link