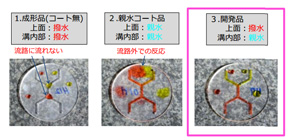
Low-cost production technology for sophisticated microreactors by surface finishing technique using water
Will lead to a wider use of DNA testing, regenerative medicine, and low-friction materials
Researchers from Osaka University and Crystal Optics Inc., developed a manufacturing method for nano- and micro-scale structures. This technology has enabled the control of the wettability of a surface by combining advanced surface microstructure and functional surface films.
Unlike conventional expensive production processes, this technology has enabled an inexpensive production process that combines technologies of fine shape transfer, film formation, and selective thin film removing. This technology will realize easy access to regenerative medicine, tissue engineering, biomarkers, and DNA testing, and lead to application to new fields, such as photoregulation.
Conventional microreactors were produced using photolithography, a process used in fabrication of semiconductor devices, printed circuit boards, printing plates, liquid crystal display panels, and plasma display panels. The process required expensive production machines; however, its productivity was low.
This group has achieved the low-cost production of high-performance microstructures, such as microreactors (Figure 1) and cell culture dishes, by applying Water-CARE (catalyst-referred etching), which enables chemical etching of surface protrusions, to fine shape transfer and thin-film coating technology.
The Water-CARE device (Figure 2) has the same composition as conventional polishing devices, but a 100 nm thick film of platinum or nickel, which functions as a catalyst, is deposited onto the surface of a polishing pad. In conventional polishing methods, protrusions of a sample are preferentially removed, yielding a smooth surface in the process in which a polishing pad rubs the surface in machining fluid containing abrasive grains and chemical agents.
On the other hand, in Water-CARE, the surface of the sample is etched by water alone without using slurry. Because a chemical reaction is induced when the surface of a catalyst comes close to the sample through water molecules at the atomic level, as in the case of conventional polishing methods, etching proceeds preferentially at protrusions on the sample where the catalyst comes into contact with the surface of the polishing pad, yielding a smooth surface.
This technology uses neither abrasive grains nor chemical agents. As machining is done with water alone, requirements of a clean room are met. This is an environmentally friendly machining technique that generates no industrial waste.
Conventional technologies required many processes and precise control -- an exposed hydrophilic coating film was etched with grooves masked and the masking layer later was removed, and an extra hydrophilic coating film on protrusions was removed by precision polishing while controlling the amount of polishing.
By using Water-CARE, this group achieved a very easy and inexpensive production method. In Water-CARE, only water is used as machining fluid and abrasive particles don’t go into grooves, so there is an advantage that the burden on the following cleansing process is reduced.
Professor Yamauchi said, “It will become possible to realize low-cost production of surfaces with various functions, such as the function to control the wettability of the surface, as well as light and friction coefficients, by using our revolutionary research results. Moving forward, our technology will be useful in achieving at-home DNA testing for cancer, diseases, and disorders. It will also lead to the development of regenerative medicine and biotechnology, contributing to energy-saving and energy creation through the use of solar batteries which decrease energy loss.”
Figure 1. High-performance microreactor produced by developed manufacturing technology
Figure 2. Schematic diagram of Water-CARE system
Related links