How to consistently nurture capricious “cells” and offer them to patients at a reasonable price?
Implementation of regenerative medical technology by “Kotozukuri”
Professor Masahiro Kino-oka, Director in Research Base for Cell Manufacturability, Techno Arena, Graduate School of Engineering, Osaka University
“Regenerative medicine” aiming to restore damaged functions by grafting the retina, heart muscle, nerves, etc. prepared from sources, such as iPS cells, is rapidly developing. The entire world is engaging in the development race by regarding it as a technology to open a way to treatment of refractory diseases without means for a radical cure. However, treatment using cells as “living things” is associated with difficulties different in nature from those of treatment using existing drugs. One is the instability of cell manufacturing, which is different from manufacturing chemical agents. Industrialization to supply high-quality cells consistently and at a reasonable prince is indispensable for the spread of regenerative medicine. In addition, society lacks the technology to mass-produce cells, or human resources or rules to properly manage the technology. Professor Masahiro Kino-oka of Graduate School of Engineering, Osaka University aims to support physicians by creating a “system optimal for cell manufacturing based on the perspective of engineering”. The keyword is “Kotozukuri” (creation of systems, stories and services from the viewpoint of the market that surrounds manufacturing) integrating the development of materials, human resources, and rules.
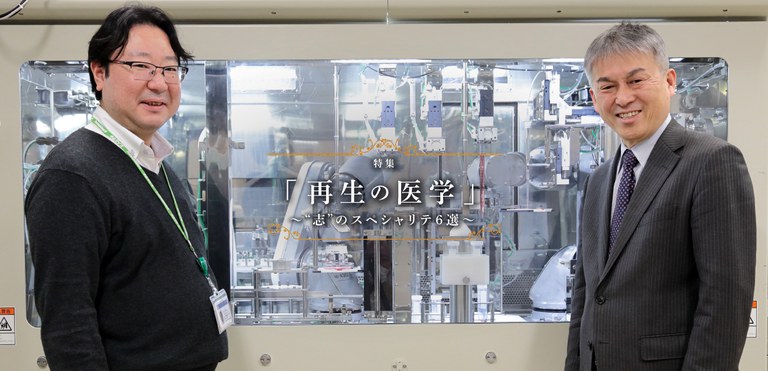
From the “hands of God” to the “hands of machines”
In an operation module installed in the center of a laboratory in Industrial Co-creation A Building at Osaka University Suita Campus, a robot arm quietly continues changing the medium to supply nutrients to cells by skillfully manipulating Petri dishes and pipettes. Arranged around it are several incubator modules to culture cells after medium replacement under prescribed conditions, and transfer modules to bring in and out cells and reagents by human hands. Each module can be connected and disconnected by maintaining a germ-free condition, and the procedure is programmed such that as soon as one operation is finished using one cell strain in the operation module, which is the heart of the system, the next operation using another cell strain can be initiated. The cost can be reduced by improving the efficiency of the operation module. Flexible shifts of work processes are made possible by the structure connecting different modules like toy blocks.
Professor Kino-oka explained that “cell culturing had the strong image of special artisanship performed by “the hands of God” of skilled experts. However, consistent culturing of a large number of cells cannot be achieved by this method. For developing the technology of regenerative medicine into an industry, it is indispensable to replace “the hands of God” by “the hands of machines” and to make the series of processes into an optimized system. We refer to this as “cell manufacturization”.
However, replacing “the hands of God” with “the hands of machines” is not an easy job.
Humans can move slowly and smoothly as in classical Japanese dancing, but cannot hold the hand stationary for a long time. In contrast, machines are good at repeating the same movement and holding still for a long time, but not at moving smoothly.
“Cells are vulnerable to impact and are damaged even by slight vibration. Therefore, we analyzed movements of experts in cell culturing using the acceleration sensor and made the robot arm imitate them. At first, the acceleration was as sharp as that of a roller coaster. Cells had no chance to survive. We gradually sophisticated the program and achieved smooth movements.”
The cost of grafting retinal cells made from iPS cells into a patient with a refractory disease in 2014 by RIKEN was approximately 100 million yen. Using the current equipment, retinal cells for approximately 250 patients can be prepared automatically in around 4 months, and the cost is estimated to be reduced to half or to around one-tenth regarding the manufacturing process alone.
Bridging between biology and engineering
In addition to the necessity of delicate work, cells are capricious, unlike conventional drugs. Professor Kino-oka compared the difficulty in controlling the capriciousness of cells and maintaining their quality to child rearing.
“Children can be nice or defiant depending on how they are talked to. Moreover, it is OK if they respond immediately when they are talked to, but in some cases, emotions accumulate inside and explode after a month. Cells behave similarly. When a drug is added, and effects may appear after a day or even a month with a “late onset”. As cells are alive and have an active metabolism, elements that constitute cells change with time, demonstrating “time-dependence”. In addition, the condition of cells cannot be measured in real time by present technology and is recognized later “with a delay”. With standard chemical products, they can be avoided if the quality of the raw materials is made constant and the process is controlled properly. However, in cell manufacturing, unexpected variability of quality occurs because the products are alive. We call this “internal variability”.
Cell manufacturing often extends over a long period, for example, several months, during which “internal variability” is likely to accumulate. To manufacture cells with consistent quality in the face of such uncertainties, it is necessary to understand both biological and engineering aspects of cells, and design the manufacturing processes to bridge them.
Furthermore, along with the rapid development of research in the field of regenerative medicine, cell manufacturing is required to meet higher and higher levels of sophistication.
At first, cells themselves were cultured, but processing of cells into sheets and arrangement of such sheets as layers are now required. In addition, manufacturing of even organoids and organs themselves is becoming a reality.
To cater to such needs, quantitative analyses of how cells behave in tissues with three-dimensional structures, for example, how blood vessels are formed in cell sheets, become important. His research group is also endeavoring to develop instruments, such as a three-dimensional cultivation simulator, with which such processes can be reproduced with the computer.
“Kotozukuri” integrating human resources, materials, and rules
On a day in mid-January 2020, 20 plus working people gathered in a room in Osaka University Suita Campus for the “Systematization Seminar” sponsored by the “Base for Cell Manufacturability”, a linkage-type fusion research organization established by the School of Engineering in 2016. Technicians from 23 business firms of a wide range of fields, including pharmaceutics, medical equipment, chemistry, optic machines, and plant building, assembled and had discussions together with Professor Kino-oka and special lecturers. The seminar was planned to be held monthly for a total of 15 times over a period of 1.5 years. The principle was that the participants report the results of their research on themes given in advance, such as “differences between drug manufacturing and cell manufacturing”, “management of sterile environments”, and “strategy for international standardization”, and exchange questions and answers among themselves and with the professor and lecturers. On this day, an employee of a major logistics company took the podium and made a presentation about the processes of cell isolation, purification, packaging, and storage. His point was “time is a great factor in the cell viability after dispensation and cell recovery rate after thawing. Consideration of such time-dependence is essential in determination of the lot size.”
Professor Kino-oka explains his aim of setting up such an arena for discussion as follows:
“There is no textbook for industrialization of technologies of regenerative medicine. We accept only 1 participant from each company and the same members participate in all 15 seminars. The objective is to have them cross company borders and develop interdisciplinary linkage. We want the participants to keep discussing with people in different positions with the aim of creating a brand-new textbook, and when they return to their companies, go ahead and share what they have discussed with their colleagues at home. They can polish up their sense about cell manufacturing through discussing and thinking.”
For manufacturing cells, which is directly linked to medical care, it is inevitable to create new regulations and rules. In this stage, they will greatly benefit from the network of people sharing the same aspiration that they have cultivated at the center.
In addition to making materials by developing core technologies for cell manufacturing, making rules for the management of regulations and international standardization, making human resources, i.e., nurturing an industrial workforce that understands the general trends and has a good sense of cell manufacturing, and “Kotozukuri” by uniting the industry, government, and academia are the keys to advance regenerative medicine.
What is research to Professor Kino-oka?
If there is a creator who creates 1 from 0, a developer who develops 1 to 100, and a keeper who keeps 100, I think I am located in between the creator and developer. If cell manufacturing is compared with cooking, I am the chef who develops a cuisine from materials and makes the recipe public.
Professor at the Graduate School of Engineering, Osaka University
Interview held in December 2019