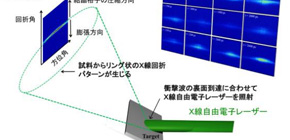
What Happens When Materials Collide? Observing Fracture in Stressed Materials
International team led by Osaka University researchers reports the first direct observations of a material’s dynamic fracture at the atomic scale, from X-ray diffraction measurements of tantalum
Osaka, Japan - Ever wondered, while cruising at 36,000 feet over the Atlantic, what would happen if a piece of satellite, asteroid, or other debris collided with your aircraft?
Dynamic fracture is the fragmentation of a material because of some stress, such as during impact. This has obvious importance for the debris shielding of materials used in aircraft, spacecraft, satellites, nuclear reactors and armor, as well as in general engineering and manufacturing.
Until now, the dynamic fracture of materials has only been observed using bulk-scale techniques, such as measuring fragment speeds or forensically examining samples. Dynamic fracture at the atomic scale could only be studied using computer simulations, since the size range that could be observed in materials by experimental techniques was too narrow. However, this has changed thanks to a new technique reported by an Osaka University-led team for directly observing dynamic fracture in metals.
The researchers have used a laser pump and X-ray probe to detect movement, such as stretching and compression, in the atomic structure of tantalum under high stress. Specifically, a laser produces a shock in a thin piece of tantalum, a metal used in alloys to increase their strength and corrosion resistance. The X-ray probe then measures the spacing of atoms in the opposite side of the tantalum. This technique is extremely sensitive to atoms near the surface, which are the ones most closely associated with surface damage.
“The evolution of lattice deformation associated with the ultrafast fracture in tantalum is given by a time series of X-ray diffraction patterns,” explains Dr. Bruno Albertazzi. “This deformation shows us the shocked part of the tantalum, which is extremely small, but the shock travels through the tantalum at nearly five kilometers per second.” It should therefore be no surprise that the tantalum’s strength becomes compromised. The measurements, carried out at the Spring-8 synchrotron complex in Japan, show a decrease in the spacing of tantalum atoms immediately before fracture. The team validates their observations by demonstrating a close match with computer simulations.
This technique can be used to investigate high-speed cracking and other stress-related effects. “This method bridges the gap in the understanding of the relationship between atomic structure and material properties,” says Associate Professor Norimasa Ozaki. Movement in a material’s atomic structure under stress can now be observed in real-time, and an important material property—the stress required for fracture— can be determined. This knowledge will benefit the design and manufacturing of equipment and technologies where resistance to impact is paramount.
Figure 1.
The schematic diagram of the experimental setup and the X-ray diffraction pattern imaging.
Thin metal foil target is driven by a shock wave generated by focused power laser (lower side in Fig. 1). Irradiating XFEL to sample behind is to observe the ultra high speed fracture phenomena. The image sequence of the X-ray diffraction snapshots with a femto-second exposure is obtained by repeatedly experiments which change the time interval between power laser and XFEL. (credit: Osaka University)
Figure 2. above: Cross section of typical spallation of a material. Big damage on the lower part of the back surface is clearly seen. Below: Distribution of space debris in earth orbit. Debris with a speed over 10 km/sec exists and may cause serious damages (on space stations and satellites). (credits: ESA & NASA)
To learn more about this research, please view the full research report entitled " Dynamic fracture of tantalum under extreme tensile stress " at this page of Science Advances.
Related links