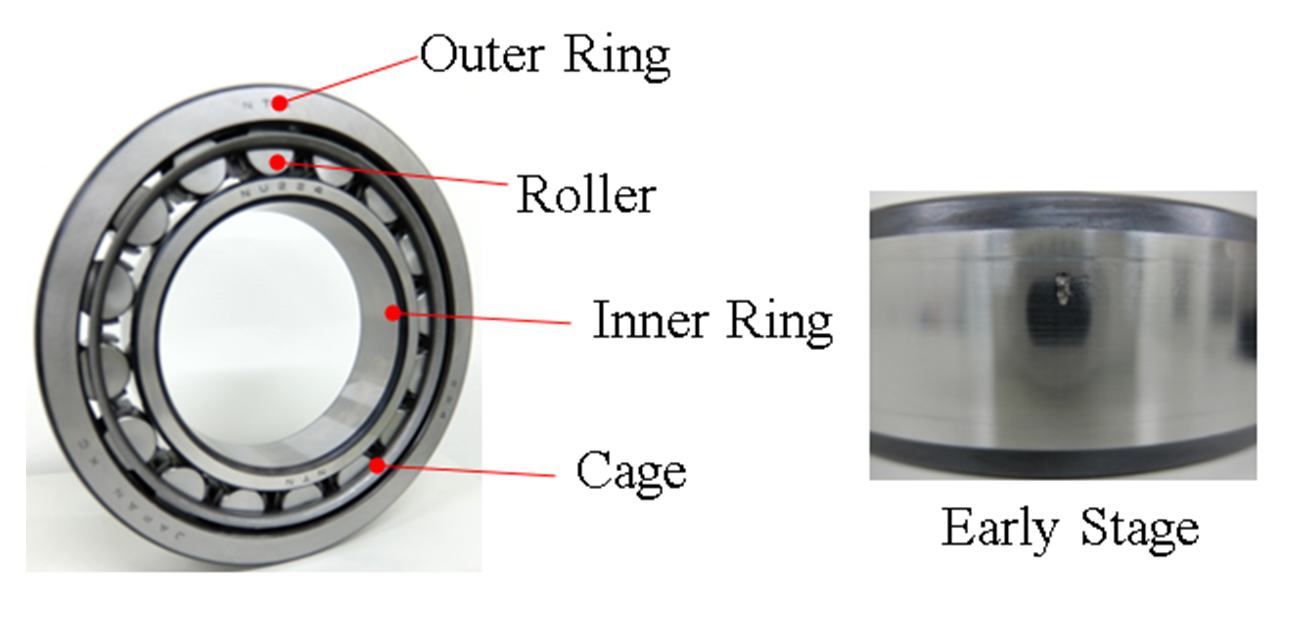
Keeping it rolling
Researchers at Osaka University employ machine learning algorithms to assess the remaining useful life of mechanical rolling bearings, which may lead to industrial cost savings, as well as fewer discarded parts
Scientists from the Institute of Scientific and Industrial Research, and NTN Next Generation Research Alliance Laboratories at Osaka University developed a machine learning method that combines convolutional neural networks and Bayesian hierarchical modeling to precisely predict the remaining useful life of rolling bearings. This work may lead to new industrial monitoring methods that help manage maintenance schedules and maximize efficiency and safety under defect progression.
A rolling bearing consists of two rings separated by rolling elements (balls or rollers). Because of the ease of rolling, the rings can rotate relative to each other with very little friction. Rolling bearings are essential to almost all automated machinery with rotating elements. The bearings eventually fail due to wear and tear, but often potential defects cannot be easily repaired because the rings are in an inaccessible place, or the machine downtime is too costly. Thus, the ability to accurately predict the remaining useful lifetime under defect progression would reduce unnecessary maintenance procedures and prematurely discarded parts without risking breakdown.
Now, a team of researchers at Osaka University have used machine learning to predict the remaining useful lifetime of rolling bearings based on the measured vibration spectrum. It is known that as defects get worse inside a bearing, its vibration amplitude begin to fluctuate. First, the scientists created a spectrogram showing the intensity of different frequencies as a function of time. These two-dimensional graphs were then used to train into a convolutional neural network, which is a machine learning method for image recognition and vision tasks.
“Predicting the remaining useful life curve of rolling bearings under defect progression is usually difficult, owing to irregular fluctuation of vibration features,” first author Masashi Kitai says. Because of this, Bayesian hierarchical modeling was used to infer the parameters, including remaining lifetime. This approach allowed the scientists to integrate the results into a single set of predictions, along with associated uncertainties. During testing, the method improved the error of predicted remaining useful life by about 32%.
“More efficient maintenance of industrial machinery based on our technology may lead to reduced environmental burden and economic loss,” senior author Ken-ichi Fukui says. Future algorithms may be generalized to work with a wide range of mechanical parts.
Fig 1. Overview of rolling bearing and defect shape on the raceway surface of the inner ring
Fig 2. Changes in the remaining life prediction distribution as defects progress
The article, “A framework for predicting remaining useful life curve of rolling bearings under defect progression based on neural network and Bayesian method” was published in IEEE Access at DOI: https://doi.org/10.1109/ACCESS.2021.3073945.