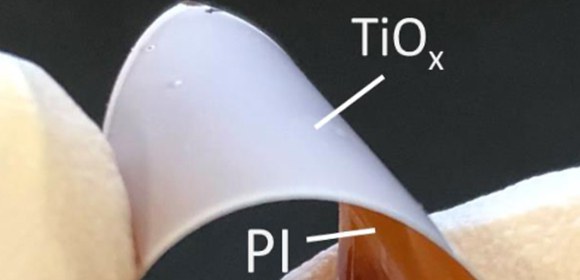
Lighting the way to porous electronics and sensors
Researchers from Osaka University introduce a straightforward fabrication method that dramatically improves the gas sensing performance of a common ceramic
Many common household items and devices have a coating that improves performance. For example, the thin Teflon coating on cookware helps prevent food from sticking to the surface. However, it's difficult to prepare—at room temperature—the strongly adhering, high-performance ceramic coatings that are commonly used in many applications, such as electronics. Now, researchers from Japan have solved this problem.
In a study published in ACS Applied Electronic Materials , researchers from Osaka University have shown how to coat glass and plastic—and presumably many other surfaces—with a thin, porous ceramic. The fabrication process is straightforward, the materials are cheap, and the ceramic's gas sensing performance is considerably improved compared with current devices.
The researchers' ceramic coating, porous titanium dioxide, is an exciting material.
"Titanium dioxide is cheap and abundant, and has many applications such as in gas sensing," explains Tohru Sugahara, senior author. "Porous films have a high surface area to volume ratio, and can detect gas analytes at lower concentrations than corresponding nonporous films."
The researchers first used spin coating to deposit a thin film—approximately 1 micrometer thick—of porous titanium dioxide onto a glass or plastic surface, in only one step. They then tested two approaches to strongly adhere their films onto the surface: high-temperature sintering for the glass, and high-intensity light for the plastic. Both approaches retain the nanometer-scale pores and strongly adhere the ceramic film.
The thin ceramic films prepared by high-temperature sintering performed remarkably compared with nonporous titanium-based gas sensors. "For example, gas detection is fast," says Sugahara. "The response time—the time required for the sensor to attain an optimum response—is approximately 1 s, whereas other sensors require a few minutes."
The researchers envision many applications of their porous ceramic coatings. For example, viruses can be entrapped in the pores. Once caught, the viruses can be destroyed by irradiating the films with UV or visible light, without damaging the films. Another application is whitening agents; the porous films diffuse a great deal of UV and visible light. Many useful applications are possible with the researchers' economical, straightforward approach to strongly adherent ceramic coatings.
Fig.1 Nanostructur porous titanium oxide thin film (TiOx) deposited on the plastic (PI: polyimide) substrate.
Fig.2 Schematic images of high-intensity pulsed light photosintering apparatus. ( Left ) Before photo-light irradiation, ( Right ) During photo-light irradiation.
Fig.3 Top/cross-sectional view of scanning electron microscopic (SEM) images of the nanostructure titanium oxide (TiO x ) thin film. ( Left ) After heat sintering, ( Right ) After photosintering, ( Top ) Top view, ( Bottom ) Cross-sectional view.
The article, "Formation of metal-organic decomposition derived nanocrystalline structure titanium dioxide by heat sintering and photosintering methods for advanced coating process, and its volatile organic compounds' gas-sensing properties," was published in ACS Applied Electronic Materials at DOI: https://doi.org/10.1021/acsaelm.0c00237 .